High temperature adhesive for refractory
The fire resistance of the rotary kiln lining commonly used at home and abroad is on the kiln wall. The masonry needs to support the formwork first, then the refractory brick is built on the kiln wall or the whole pouring. The operation is cumbersome, time-consuming and laborious, and the kiln lining The combination with the kiln wall is not tight enough. The rotary kiln is constantly rotating during the use, the vibration is strong, the working environment is bad, the refractory brick is easy to be stripped, and the kiln lining has a short service life. In addition, the general refractory kiln lining is only resistant to fire resistance, and the refractory brick has a large thermal conductivity, and the heat loss in the kiln is large, which wastes energy. Now it provides a simple structure, no need to use template in construction, convenient masonry, tight combination of brick body and kiln wall, not easy to draw and peel off, long service life of kiln lining, and can reduce heat loss in kiln and save energy. brick. The addition of a high temperature binder can increase the strength and high temperature resistance of the refractory brick.
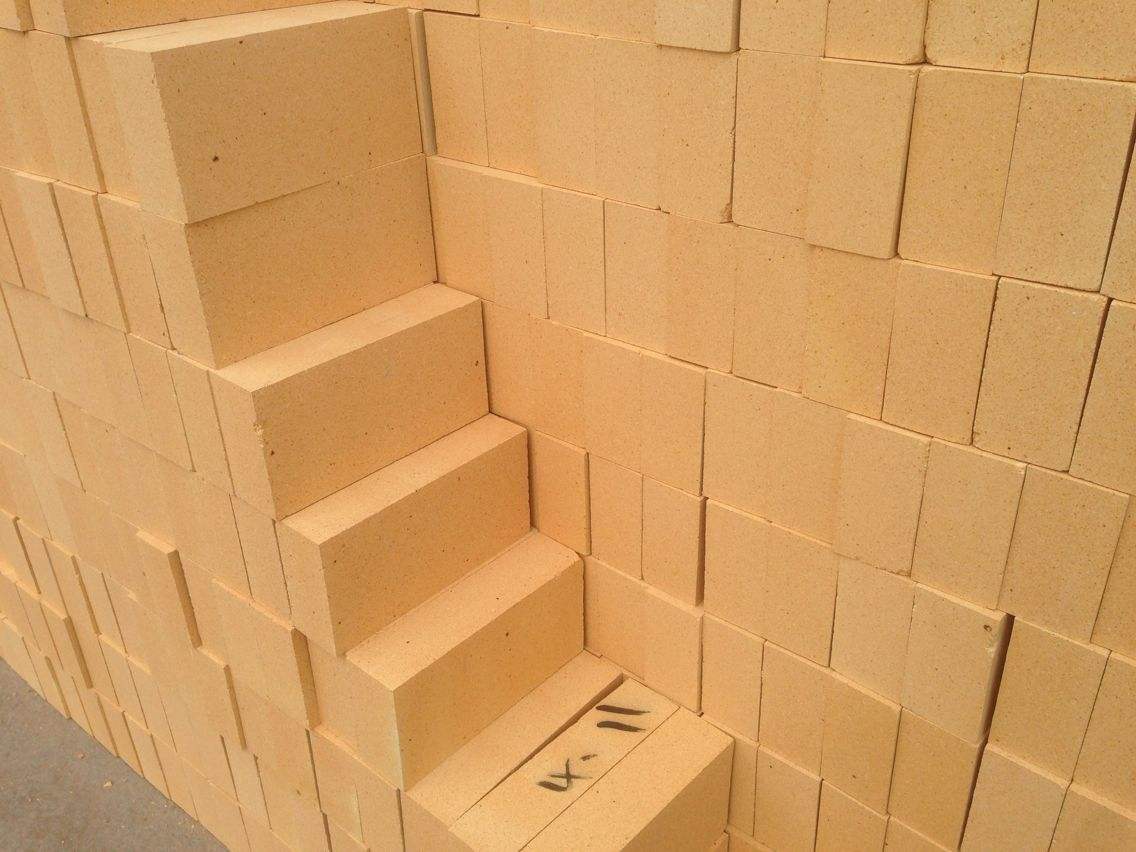
High temperature adhesive for refractory brick
How to form refractory bricks, in order to reduce the porosity of refractory bricks and improve the quality of refractory bricks, it is necessary to increase the molding pressure. For ordinary refractory bricks, the forming force should reach 137 MPa: the forming force of high-density refractory bricks should be in the range of 176-215 MPa. In other words, this effect can only be achieved by molding with a squeezing brick press of 250t or more. The porosity of refractory bricks should meet the following requirements ≤23%. The refractory bricks are formed and dried. The moisture content of the slabs after molding is generally above 3.5%. It can not be immediately kiln-fired and needs to be dried to reduce moisture. The drying system of the green body varies depending on the molding method of the green body and the single weight. The green body formed by the semi-dry method should be dried in a tunnel drier. The hot air temperature is 140-160 ° C, the exhaust gas temperature is 60-90 ° C, and the residual moisture of the blank should be less than 2%. The blanks formed by hand molding, hammer hammering and vibration molding should be naturally dried first. The drying time varies depending on the weight of the individual. For a blank weighing less than 10Kg, it can be naturally dried for 16~24h: 10~25Kg, naturally dried for 36~40h, for a single weight of 25~40kg, naturally dried for 72~96h. During the month of the blank, the natural drying time should be longer. The naturally dried body can be dried in a desiccator. The hot air inlet temperature of the dryer is 100~120°C: the exhaust gas temperature is 60~80°C. What is the most important problem? When fired in a downdraft kiln, the general firing temperature is 1390~1400 °C, and the heat preservation is 24~32h.